Different Specifications of Extruded Activated Carbon: Find the Perfect Pellet Size & Grade
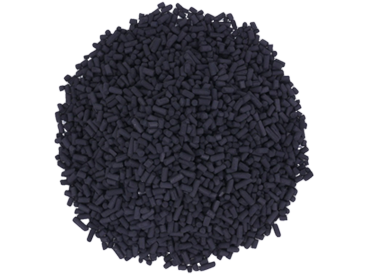
Our Pellet Activated Carbon, produced via high-temperature steam activation with carefully selected binders and stringent quality control, offers exceptional absorption capacity. This enables effective removal of diverse contaminants from air and gas streams, solvent recovery, and control of evaporative emissions. Specifically designed for vapor phase applications, it addresses vapor remediation, VOC removal, soil venting, and the elimination of organic substances such as ammonia, sulfur compounds, mercury, and amines.
Extruded Activated Carbon: Material Used
Extruded activated carbon (EAC) is manufactured by binding fine powder activated carbon particles together to form cylindrical pellets. The primary component, of course, is the activated carbon itself, which originates from the same carbonaceous source materials as other forms of activated carbon. These include:
- Coal: Often bituminous coal, chosen for its specific properties that yield a durable extruded product suitable for gas phase applications.
- Coconut shells: Can also be used, resulting in a harder, more microporous extruded carbon often preferred for certain liquid phase applications.
- Wood: Less common for extruded forms but can be utilized, potentially offering different textural and adsorption characteristics.
Production Process For Extruded Activated Carbon
The powdered activated carbon used as the base material is produced through the standard two-step process of carbonization and activation (either physical or chemical), as described for granular and powdered activated carbon. The key difference in EAC production lies in the agglomeration or binding process that forms the pellets.
To create the extruded shape, the fine powder activated carbon is mixed with a binder. Common binders include:
- Clay: Provides structural integrity and is a cost-effective option.
- Lignosulfonates: These are natural polymers derived from wood pulp and act as effective binders.
- Starches: Another natural binder option.
- Synthetic polymers: In some specialized applications, synthetic binders may be used to achieve specific properties like chemical resistance.
The mixture of powdered activated carbon and binder, along with water or other solvents to create a workable paste, is then fed into an extruder. This machine forces the mixture through a die with small, circular openings, forming continuous cylindrical strands. These strands are then cut to the desired length to create the pellets.
After extrusion, the pellets are typically dried to remove excess moisture and solidify the binder. In some cases, they may undergo a further curing or heat treatment stage to enhance their hardness and durability.
The resulting extruded activated carbon pellets have several advantages. Their uniform shape allows for consistent packing in filters and adsorption beds, minimizing pressure drop and channeling. The extrusion process also creates a mechanically strong product with low dust generation, making it ideal for applications involving gas flow and repeated handling. The specific properties of the EAC, such as pellet diameter, length, surface area, and pore size distribution, are controlled by the choice of raw material, activation method, binder type and concentration, and the extrusion process parameters.
Beyond Expectations: Quality, Service, and Enduring Value: We strive to exceed your expectations in every interaction. From the superior quality of our products to our exceptional customer service and the enduring value our solutions provide, we are committed to your complete satisfaction.