Unwashed Powder Activated Carbon: Explore Our Range of Mesh Sizes & Properties
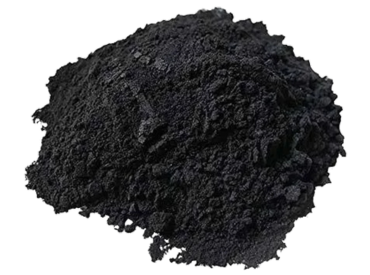
Our Activated Charcoal effectively eliminates undesirable color, odor, and impurities due to its exceptional diffusion properties and high microporosity. As a trusted manufacturer in India, we produce this highly effective deodorizer, decolorizer, and purifier under strict atmospheric control, overseen by our experienced experts.
Unwashed Powder Activated Carbon: Materials Used
Unwashed powder activated carbon begins its life as various carbon-rich organic materials, similar to other forms of activated carbon. Common raw materials include:
- Coconut shells: Favored for their hardness and ability to produce microporous activated carbon.
- Coal: Different ranks of coal (bituminous, lignite, anthracite) yield activated carbons with varying pore structures.
- Wood: Offers a broader range of pore sizes in the final product.
- Agricultural byproducts: Such as bamboo, nutshells, and other plant-based waste, providing a sustainable source.
Unwashed Powder Activated Carbon: How Is It Produced?
The initial production stages mirror those of standard activated carbon. First, the chosen raw material undergoes carbonization. This involves heating the material in an oxygen-deficient environment at high temperatures (typically 600-900°C). This process pyrolyzes the organic matter, driving off volatile compounds and leaving behind a carbonaceous char with a basic porous structure.
Next comes activation, the crucial step that develops the extensive pore network and high surface area characteristic of activated carbon. Activation can be achieved through:
- Physical Activation (Thermal Activation): The char is exposed to oxidizing gases like steam or carbon dioxide at high temperatures (800-1100°C). These gases react with the carbon, creating and expanding pores.
- Chemical Activation: The raw material or char is impregnated with a chemical agent (e.g., phosphoric acid, potassium hydroxide, zinc chloride) and then heated at lower temperatures (400-700°C). The chemical aids in pore development.
The key differentiator of “unwashed” powder activated carbon is the omission of the acid washing stage. In the production of acid-washed activated carbon, a post-activation step involves washing the material with an acid solution (like hydrochloric acid) to remove residual ash, heavy metals, and other inorganic impurities introduced from the raw material or the activation process.
Unwashed powder activated carbon skips this acid washing step. After activation (either physical or chemical), the carbon material is typically rinsed with water to remove loose particles and any residual chemical activating agent if chemical activation was used. It is then dried and ground into a fine powder to increase its surface area-to-volume ratio, making it suitable for applications where rapid adsorption kinetics are important.
The absence of the acid wash means that unwashed powder activated carbon may contain a higher concentration of ash, water-soluble salts, and potentially trace amounts of heavy metals compared to its acid-washed counterpart. The surface chemistry might also be different due to the presence of these residual inorganic components. Consequently, unwashed powder activated carbon is generally used in applications where these impurities are not critical concerns or where the cost-effectiveness of the unwashed material outweighs the need for higher purity.
Solutions You Can Depend On, Expertise You Can Rely On: Navigating the complexities of industrial supplies requires expertise. Our team possesses in-depth knowledge of our product range and industry best practices, providing you with reliable guidance and ensuring you select the right solutions for your specific requirements.